5 essential tips to improve gas sensor performance and life expectancy
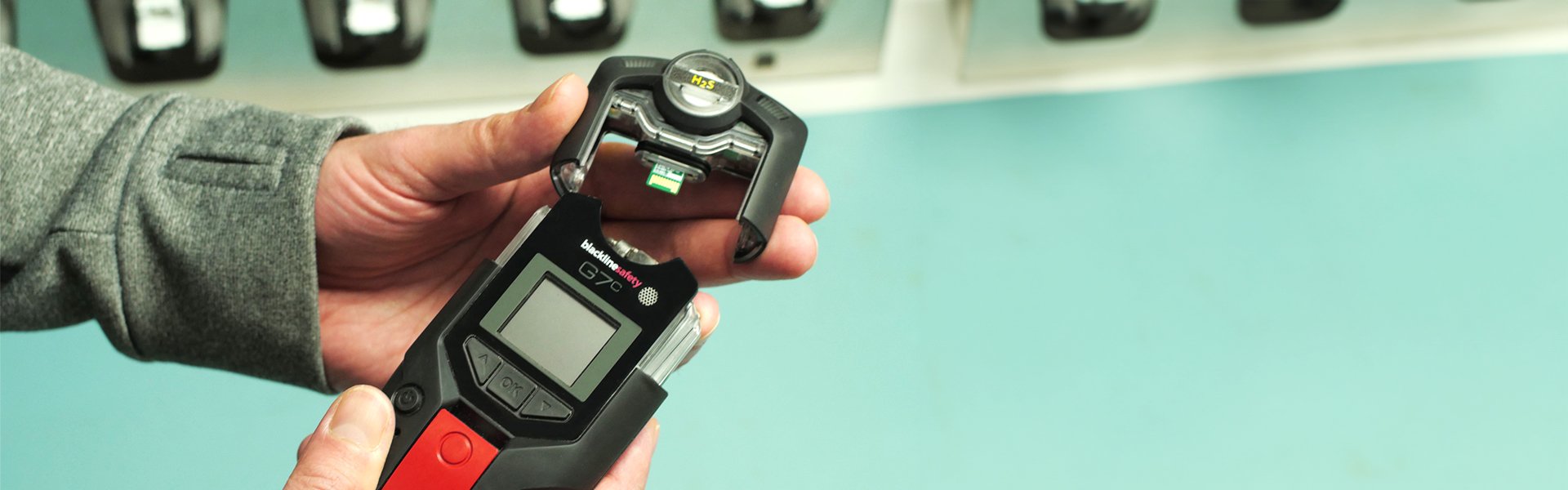
Gas sensors typically last between 6 months and 4 years, but their lifespan and performance vary based on the factors and conditions they are exposed to. 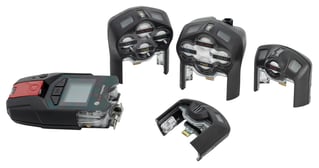
Understanding the ideal conditions for your sensors—including how different environmental and operational factors impact them—can help you implement prevention and mitigation strategies to optimize sensor performance.
Five ways you can optimize your gas sensors and increase their life expectancy:
- Understand How Temperature Affects Your Sensors
- Tailor Your Storage Space to Your Sensors
- Train and Engage your Team
- Proactively Maintain Your Sensors
- Prevent Common Sensor Issues
Understanding How Temperature Affects Your Sensors
Getting the most out of your sensors begins with understanding how the environmental and operating conditions that your sensors are exposed to impact their overall performance and life expectancy.
Extreme weather impacts your area monitor by reducing battery life, causing sluggish responses from the device, or even resulting in false readings. Very hot and dry conditions can also age electrochemical sensors by causing the electrolyte to dry out.
Generally, the ideal conditions for the four different sensor technologies are:
- Temperature – 20⁰C
- Humidity – 50%
- Pressure – 100kPa
Each sensor type—PID, NDIR, Electrochemical, and Molecular property spectrometer (MPS)—has its strengths and weaknesses. Factors like sensitivity, selectivity, and response time can vary under different conditions.

Evaluate the operating environment you will be working in when selecting the sensor types. Take into account how elements in your environment and operating conditions might affect the sensor’s performance.
For example, the temperature and humidity of where your sensor is used can affect your sensor’s ability to accurately measure gases. High humidity or sudden changes in temperature can cause moisture to form on or within the sensor, which can lead to baseline drift or to sensor failure.
Consider how local environmental changes might impact your sensor to develop strategies that minimize the impact to your sensors.
Tailor Your Storage Space to Your Sensors
Be proactive about controlling the space where you store your sensors to extend their life expectancy. Keep your devices in a known, clean, temperature-controlled space to minimize exposure to unexpected elements. Interactions with dust, dirt, cleaning products, alcohol, or solvents can impact your sensor’s performance.
Also, consider how electronic devices near your sensors may affect them. For instance, some batteries release hydrogen while charging, and may expose your sensors to hydrogen if they are stored nearby.
Keep the area around your devices clear to prevent unexpected interactions with your sensors.
Training and Motivating Your Team
Empower your team by understanding your sensors and developing training programs to support their use and maintenance. Regular training sessions on how to clean your device properly, change its filters, and ensure correct device placement are crucial. PID sensor lamps, for example, should be cleaned out to remove dust or other airborne particles that interfere with the sensor’s output.
Encourage your workers to ask questions, as it can help you to identify gaps in understanding and ways to update your procedures.
You can also encourage your frontline managers to communicate the importance of your sensor maintenance to their teams, this can motivate workers to take ownership over the care and condition of the devices. Sharing your organization’s successes in prevention and incident resolution can go a long way toward motivating your team to take better care of their sensors.
Our recent whitepaper Change Management: Connected Safety Technology Adoption details practical tools and strategies you can use to engage leadership and workers on optimizing gas sensor performance.
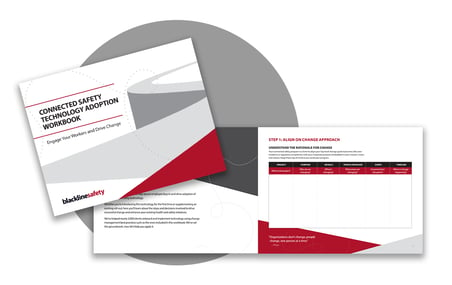
Be Proactive in Maintaining Your Sensors
Adhering to a regular maintenance schedule has a big impact on your sensor’s life expectancy. Regular maintenance confirms that your sensors are working as expected and identifies potential issues in the sensor’s performance early on.
To get the best use out of your sensors, your regular maintenance should include the following procedures:
- Regularly clean devices with water and mild soap.
- Keep your devices charged.
- Replace gas sensor filters when they become visibly soiled or if bump tests and calibrations fail repeatedly.
- Clean PID sensor lamps when the output degrades.
- Calibrate your device after replacing the gas sensor filters or cleaning PID sensor lamps to restore the sensor’s equilibrium.
For more information on cleaning PID sensor lamps, refer to the PID Sensor Lamp Cleaning Procedure. 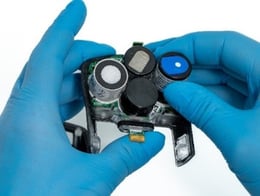
Regularly bump testing and calibrating your devices is also a crucial part of sensor maintenance. Bump testing and calibration confirm that your sensors and notification indicators are all working as they should, especially when your sensors are beyond the typical life expectancy.
Blackline recommends that you do not exceed 30 days between bump tests or 180 days between calibrations or sooner based on your standard operating procedures.
Prevent Common Sensor Issues
Knowing why and how common sensor issues occur helps you to be proactive in preventing them. Some examples of common sensor issues are:
Cross-sensitivity
Cross-sensitivity is when a sensor reacts to a non-target gas. There are two common types of cross-sensitivity: inhibition and poisoning.
- Inhibition is when a non-targeted gas, like car exhaust or alcohol, temporarily affects the output of a sensor. You can recover the output of your sensor by purging the sensor with a known gas or by waiting for the contaminant to dissipate.
- Poisoning is when a sensor’s output is permanently affected following exposure to certain chemicals or environmental factors, such as solvents or harsh cleaning products.
For more information on cross-sensitivity, refer to Gas Sensor Cross Sensitivity.
High Gas Exposure
When a sensor is exposed to a high concentration of gas, it can affect the calibration cure and sensor’s ability to measure gas, leading to inaccurate readings or cause the sensor to fail.
Baseline Drift
Sensors baselines can drift, causing the sensor to read zero incorrectly. A common cause of baseline drift is not following the order of calibration during a bump test or calibration. For more information on the order of calibration, refer to G7 and G7 EXO Gas Sensor Bump Testing and Calibration Order.
Baseline drift can also occur when a sensor is not regularly maintained. A build-up of dirt, old filters, or unclean PID lamps can often lead to inaccurate readings.
Sensor Failure
Sensor failure occurs when a sensor is unable to accurately measure gas levels, or the output of the sensor is permanently reduced. Failed sensors do not always mean that the device has failed. In most cases, changing the cartridge will resolve the issue.
Every second counts during a gas exposure and well-maintained gas sensors respond faster, reducing the number of incidents and improving overall worker safety.
Additional Resources
Sensor Cross-Sensitivities - Print Ready File
Sticky Gases Reference Sheet